Report on the 22nd Inno-Meeting on February 12 and 13, 2025 in Osnabrück
Flexpack minimal packaging – trends and technologies 2025
According to the motto “Less is more”, the 22nd Inno-Meeting presented future-oriented and sustainable approaches in the development of flexible minimal packaging. From 12 to 13 February 2025 in Osnabrück, the symposium showed how innovative design, new materials and state-of-the-art technologies can minimize the use of resources in packaging and reduce the impact on the environment without compromising on functionality or aesthetics.
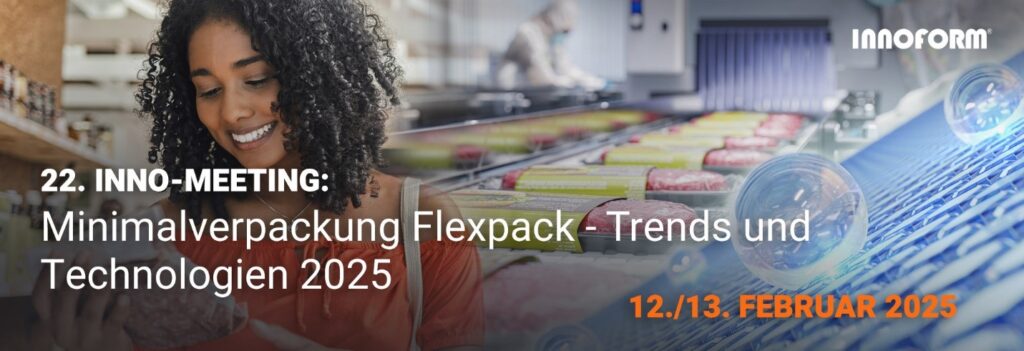
At a time when environmental protection is essential, the optimization of packaging is a social necessity. This is reflected in legal requirements to which the industry provides answers. The 22nd Inno-Meeting in Osnabrück showed which minimalistic packaging solutions have been developed as a result. As organizer and moderator, Karsten Schröder led the participants through an inspiring program according to the motto “Minimum Packaging Flexpack – Trends and Technologies 2025”, providing them with valuable impulses and engaging them in lively discussions.
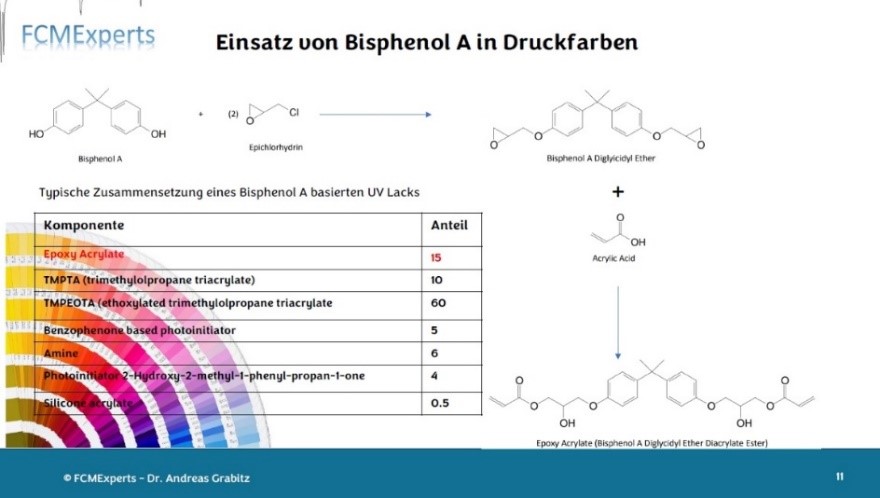
Example of the use of bisphenol A in printing inks, which will be banned. (Source: FCMExperts)
Dr. Andreas Grabitz from FCMExperts gave an overview of the “Regulatory Challenges 2025” for food contact materials and presented key points of Regulation (EU) 2024/3190. This largely bans bisphenol A (BPA) and other bisphenols classified as hazardous. Manufacturers must issue declarations of conformity, while a few exceptions are subject to very strict requirements.
He also addressed the PPWR 2025/40, which sets PFAS limits, bans applications such as pizza boxes and classifies packaging into three levels. From 2030, all packaging must theoretically be at least 70 % recyclable. From 2035, this must also be implemented on an industrial scale. From 2038, this proportion will be increased to 80 %. In addition, binding quotas for the use of recycled plastics in certain packaging will be prescribed, which will require new materials and processes.
Ralf Küsters from LyondellBasell Industries presented alternatives to fluorine-based processing aids. The PFAS compounds used in these led to the start of various bans within the EU. For the different requirements in blown and cast film extrusion, the company has developed a product range called POLYBATCH PPA, which replaces fluorine-based processing aids. This range contains products that improve polyethylene processing by preventing melt fracture, e.g. in LLDPE blown film extrusion, or by reducing the material build-up at the die during the extrusion of LDPE and LLDPE films. The product range is compliant with the food law requirements in the USA (FDA) and the EU authorities.
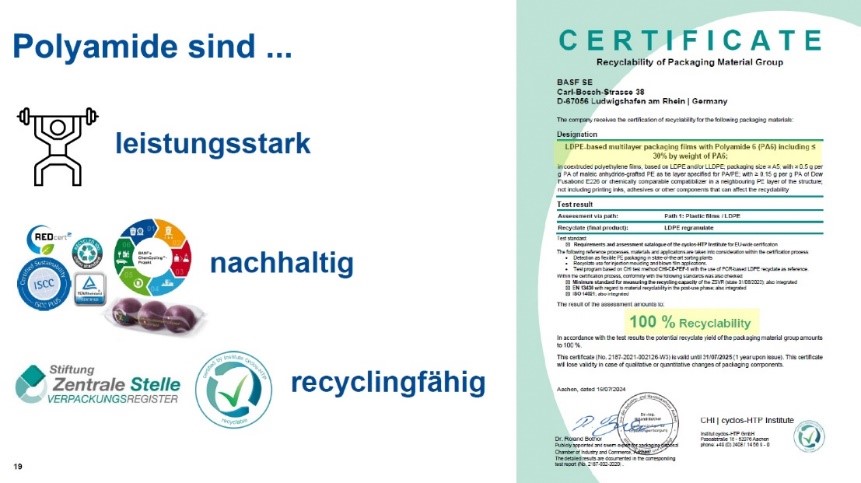
Certified recyclability of polyamide through adapted design (D4R). Source: BASF SE)
Simone Schillo from BASF SE presented scientifically based facts on BASF’s sustainable polyamide portfolio as well as convincing arguments on the recyclability of multilayer packaging containing polyamide. The use of polyamides makes an important contribution to the conservation of resources, as packaging waste can be reduced by using thinner versions of multilayer packaging.
Studies by the independent institute cyclos-HTP GmbH show that coextruded PE/PA films equipped with adhesion promoters (PE-g-MAH) can be integrated into existing PE recycling streams without any process adjustments. As a result, polyamides do not represent impurities in the mechanical recycling process, but are valuable materials that promote sustainable packaging solutions and the circular economy. In certain cases, PA-PE recyclates can even make today’s PE films without recyclate stronger.
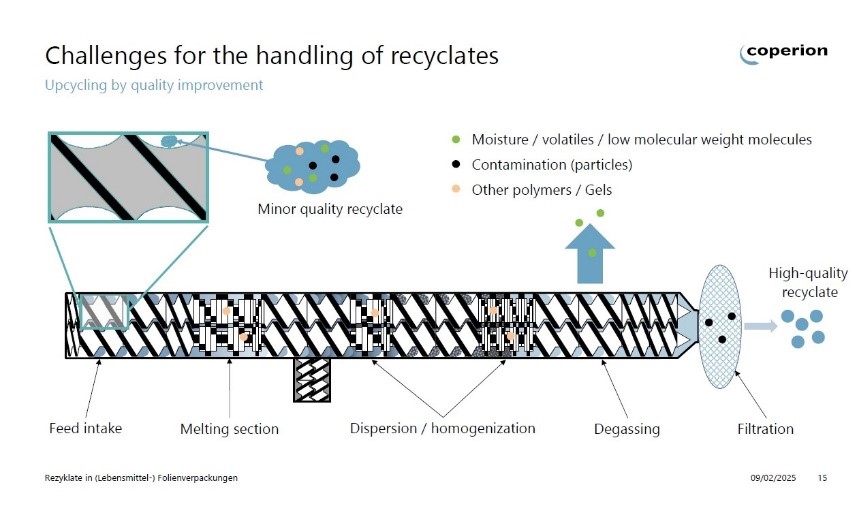
The ZSK twin-screw extruder reduces gel formation by up to 90 % thanks to an optimized shear profile. (Source: Coperion GmbH)
In his presentation “Recyclates in (food) film packaging”, Leonid Liber from Coperion GmbH explained the challenges of recycling plastic films. The focus of the presentation was on the areas of material handling and compounding. Thanks to the patented ZS-B MEGAfeed side feeder, film flakes with a low bulk density can be fed reliably and gravimetrically to the ZSK twin-screw extruder. There, the optimized shear profile reduces gel formation by up to 90 %, degasses volatile components and thus optimizes the film quality. Optimized sorting, processing and possible additives produce high-quality recyclates that can replace primary plastics in (food) packaging.
Dr. Elisabeth Pinter from the Austrian Research Institute for Chemistry and Technology (OFI) illustrated the analyses behind the testing of food packaging recyclates in her presentation, which she joined from Vienna. Due to the large number of possible impurities, the decontamination efficiency of the processes must be checked using challenge tests and extensive monitoring. This is done using chemical analysis in combination with in-vitro bioassays, among other things.
In the SafeCycle research project, over 600 plastics made from virgin and recycled materials were examined. Some samples showed conspicuous effects in the Ames test, such as nitrocellulose-based paint systems after recycling, but these were not the only source of effects. Deinking/delabelling is a possible solution, for which further research is required and planned.
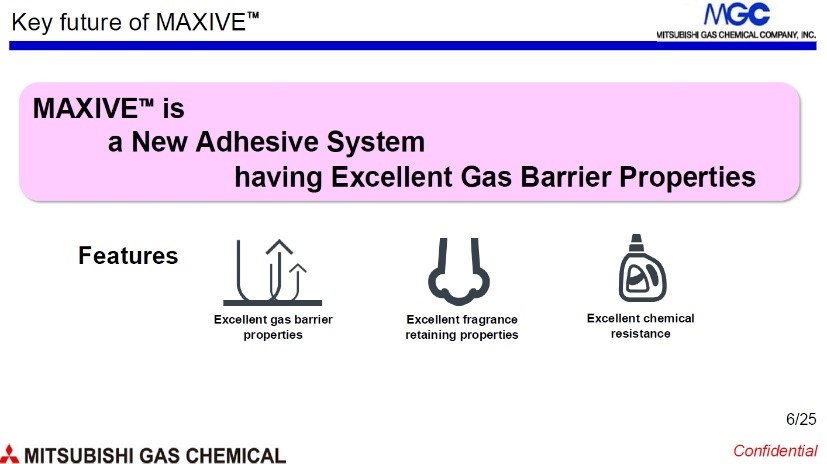
Properties of the Maxive barrier adhesive in food packaging. (Source: Mitsubishi Gas Chemical Company, Inc.)
Naoko Kobayashi from Mitsubishi Gas Chemical presented the use of the MAXIVE™ barrier adhesive for mono-material packaging in her presentation. Based on 2K poly-epoxy and polyamine resins, it offers excellent gas barrier properties, outstanding fragrance-retaining properties and high chemical resistance. As a solvent-based laminating adhesive, it achieves barrier values of conventional high-barrier composites with better recyclability. Thanks to its high resistance, it is suitable for food and cosmetics packaging. The barrier adhesive was developed for European recycling standards and is currently in the certification phase. It reduces material use and environmental impact and represents a sustainable alternative to conventional medium/high-barrier laminates with EVOH, AlOx, metallization, etc. Is this the long-awaited game changer?
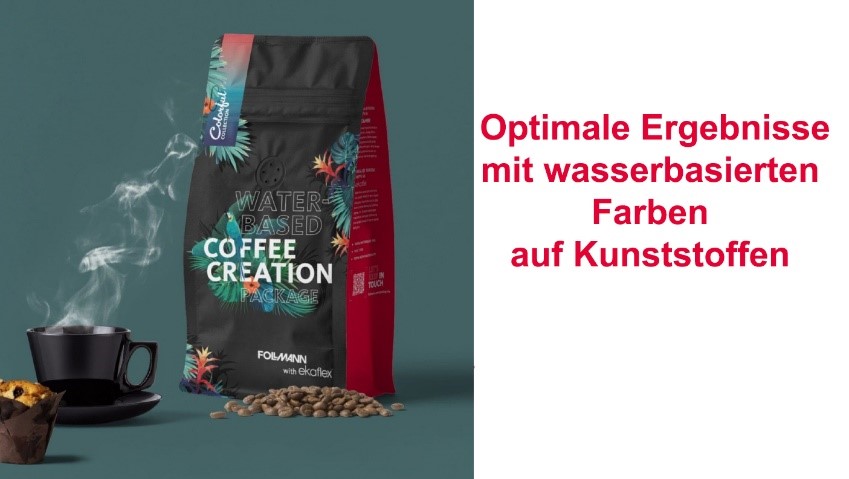
Water-based ink systems are also highly efficient for composite packaging. (Source: Follmann GmbH & Co. KG)
André Altevogt from Follmann GmbH & Co KG presented the advantages and challenges of water-based printing inks. These are environmentally friendly, VOC-free and enable high-quality printing on paper and plastic packaging. He refuted prejudices such as high purchasing and energy costs, poor print quality, odor and higher cleaning costs. Modern systems meet the same machine requirements as solvent-based inks and achieve speeds of up to 800 m/min. They also improve recycling by reducing speck formation and odor, which increases their sustainability in packaging printing. Follmann provides expert support for interested parties during the necessary change process for solvent systems.
Frederik Petzold from Windmöller & Hölscher KG presented a concept study on the development of recyclable coffee packaging, which was carried out together with Siegwerk and Saueressig. The aim was to replace conventional triplex composites made of PET/Alu/PE with a mono-material solution based on MDO-PE with an EVOH barrier. The challenges concerned gravure printing capability, temperature and web tension management as well as the choice of ink system. Technical solutions such as Supergrip guide rollers and precise chill roller temperature control as well as precise register control improved processing. The PU ink system required adjustments to avoid scumming in the highlight area. The field test showed successful printing results at 400 m/min printing speed in gravure printing and confirmed the potential of MDO-PE as a sustainable packaging solution.
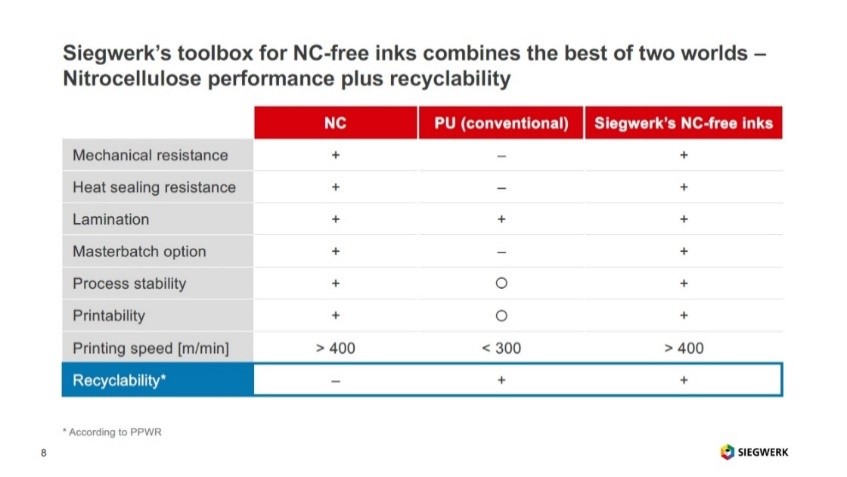
Siegwerk’s innovative PU-based ink series combines the advantages of NC systems with recyclability. (Source: Siegwerk Druckfarben)
Eugenia Spies from Siegwerk presented the status quo in the “recycling of printing inks ” for flexible packaging. Due to new EU regulations, inks containing NC and PVC are being restricted. Siegwerk has developed an innovative PU-based ink series that combines the advantages of NC systems in terms of durability, printability and printing speed with recyclability and complies with the RecyClass directives and their implementation requirements as well as the German minimum standard. In addition, the CirKit ClearPrime DP 6300 deinking primer enables efficient decoloring for transparent recyclates.
In his presentation “Prepress and printing cylinders for more sustainability in the printing process “, Ingo Büning explained how Saueressig, as a repro service provider and printing plate manufacturer, supports customers in the development of sustainable packaging. In the concept study with W&H and Siegwerk, this was achieved through an optimized, reduced packaging design, the use of 7C colour systems and gold images without metallic inks. In gravure printing, specially adapted cylinder specifications ensured minimal ink application, preferably with PU inks, which improve the recyclability of mono-material packaging. The durability of the gravure cylinders also increases efficiency. Lightweight cylinders reduce the amount of material used, while the fully digitalised cLynx final inspection does not require any ink or printing material.
Thomas Fickler from Multivac demonstrated the advantages of the innovative Cooling@Packing system for packaging baked goods. In contrast to conventional spiral and tunnel cooling, it uses vacuum for immediate cooling. When vacuuming a chamber, the product’s own moisture in the baked goods is evaporated and the evaporation energy is used to cool and package the baked goods immediately after baking. This shortens process times, saves energy, reduces space requirements and increases production capacity. In addition, immediate packaging extends the freshness and shelf life of the products by preventing contamination. Baking the crust to release the moisture can also be avoided, as this is evaporated in a vacuum for cooling.

Barrier properties of cycloolefin copolymers (Source: Topas Advanced Polymers GmbH )
Dr. Dirk Heukelbach from TOPAS Advanced Polymers GmbH presented the advantages of cycloolefin copolymers (COC) for sustainable packaging solutions. Thanks to their high rigidity, temperature resistance and excellent barrier properties, they enable high-performance mono-material packaging. As additives in plastomers, they improve sealing layers, reduce friction and optimize machine running properties. In thermoforming, they increase mouldability and reduce the shrinkage of polyolefins. COCs are fully recyclable in PE and PP streams and enable material savings through downgauging. Supply bottlenecks will also be a thing of the past from 2026 thanks to the new plant in Leuna.
Benjamin Pott from Reifenhäuser Cast Sheet Coating analyzed the potential of cast films with MDO technology for recyclable packaging, in particular mono-material stand-up pouches made of PE and PP. MDO technology improves the strength, rigidity and barrier effect of the films and optimizes thermal stability and appearance. Particularly remarkable are recyclable films with an EVOH barrier that meet future recycling guidelines. MDO-optimized films enable easy opening without laser perforation. In production, material waste and material costs are reduced thanks to the patented encapsulation in the feed block, and edge trim is returned inline. Demand for MOPE films as an alternative to BOPET is expected to rise strongly by 2030.
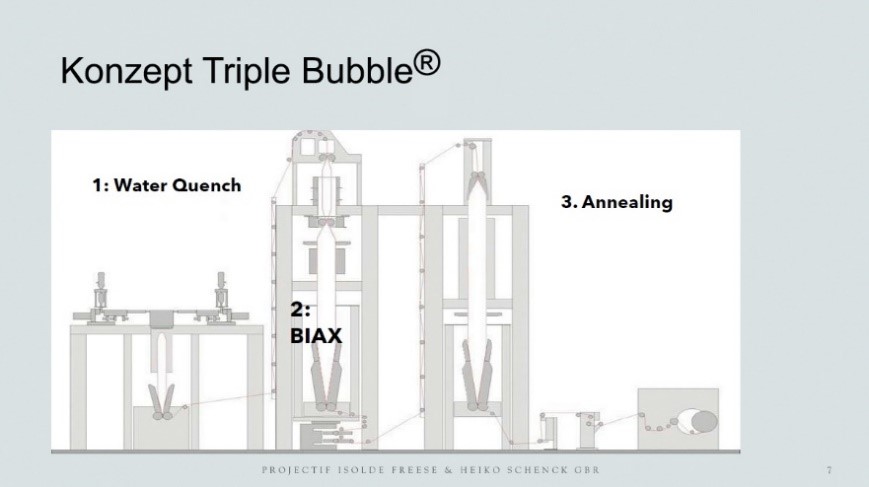
The Triple Bubble® concept consists of the serial arrangement of three bubbles. (Source: Projectif)
Dr. Heiko Schenck from Projectif presented the Triple Bubble® concept, which allows a 50 % reduction in film weight without compromising on properties. It consists of a serial arrangement of three bubbles. In the first, the film is rapidly cooled using water quench technology, which very effectively prevents crystallization processes. This is a prerequisite for uniform biaxial stretching in the second stage, which significantly improves the mechanical and barrier properties of the films. The thermal relaxation in the third bubble (annealing) is used to set the desired shrinkage behavior of 0 to 70 %. The output of a triple bubble system with a width of 6 meters is 2 tons/hour. This technology not only improves the mechanical properties, it also significantly reduces material use, costs and potential EPR charges.
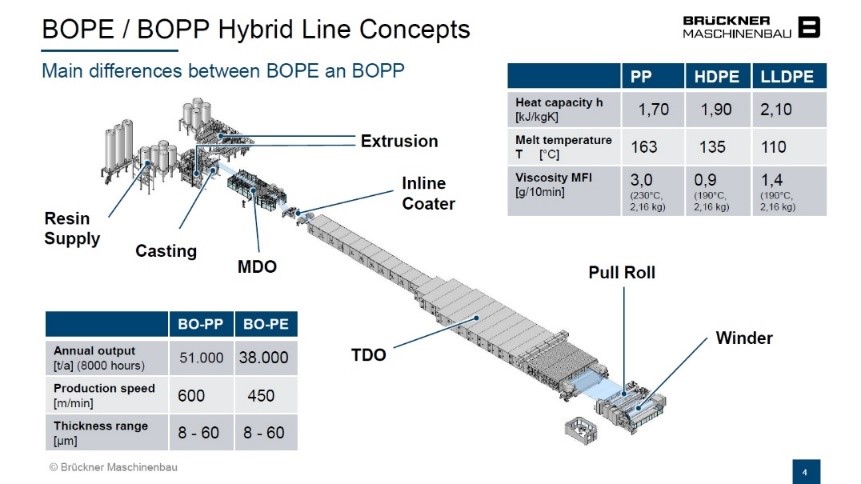
Main differences in the biaxial stretching of BOPE and BOPP films. (Source: Brückner Maschinenbau)
Dr. Stefan Seibel from Brückner Maschinenbau GmbH explained the “simultaneous, biaxial stretching of polyethylene for mono-packaging ” and presented a hybrid line concept for BOPE and BOPP.
PE mono-material packaging consists of a BOPE-HD base film, a BOPE-HD barrier film and a BOPE-LLD sealing layer and offers high transparency and good mechanical properties. BOPE-ILC films for AlOx vapor deposition and BOPE-EVOH films with barrier coating are currently under development. Other research projects include BOPE white opaque films for labels and cold seal applications, highly tear-resistant TDO-PE-HD films and films for thermoforming. These innovations underline BOPE’s potential for sustainable packaging applications.
Prof. Dr. Markus Schmid from the Sustainable Packaging Institute (SPI) at Albstadt-Sigmaringen University of Applied Sciences presented research results on plastic-free films and coatings. The focus is on bio-based materials such as proteins, polysaccharides and lipids from food by-products as a sustainable alternative to plastics.
In future, production is to be carried out in a roll-to-roll process to enable scaling. The mechanical stability and barrier effect pose challenges. The “BioShield” research project is developing new formulations and processes for improved recyclability. Together with industry partners, SPI is driving forward the development of circular packaging solutions.
Karsten Schröder closed the 22nd Inno-Meeting with a concise summary of all the presentations. In its compactness, the symposium showed that minimum packaging is not only a trend, but the future. Innovation, exchange and collaboration are driving the sustainable solutions that are required and shaping the packaging world of tomorrow.
Dieter Finna