One thing is clear in Würzburg on 22 and 23 June 2023 – The mega trend in the packaging sector – recyclability – is also and especially affecting barrier films.
Based on presentations on food waste and the guiding principle of sustainability itself, it quickly becomes clear – barrier films will continue to drive the flexpack market. The 3 pillars of sustainability: economy, ecology and social issues must be taken into account in a more balanced way, says Hilmar Heithorst. We are currently focusing on recycling and thus on ecology, but if this is not also implemented socially and economically, it is not sustainable.
The primary task of packaging as a whole is to avoid food waste, emphasises Thomas Gröner. It is a shame that about one third of the food produced is not eaten. Some of it still spoils on its way from the field to the plate because barriers are missing and supply chains are too long. Here, too, Flexpack can help to avoid CO2 emissions.
Peter Olbrich has solutions for this with his vacuum coating systems and a lot of know-how to produce wafer-thin barrier layers of aluminium, aluminium oxide (transparent) and silicon oxide. Here there are market-driven systems for the production of extremely inexpensive and meanwhile also robust barriers against oxygen and water vapour. And the best thing is that these layers, which are only a few nanometres thin, do not interfere with any of the previous recycling processes, so that the polymeric carrier layers can be recycled and reused. Only metallisation leads to a slight greying of the rain protection films – “grey is the new green”.
Stefan Schiessl presents the Fraunhofer development results around nanocomposites, which can be used as barriers on paper, among other things. The systems, which can be applied with common painting and coating processes, are also recyclable and some of them are already commercially available.
Ben Raven is aiming in the same direction with its polyethylenes for mono- and even biaxially oriented PE films. Mono-material instead of multi-material for even better recycling of film packaging. New here are PE types with higher density for the recycling process, which can be recycled mechanically and chemically without problems.
Jiabril Gigli relies on aqueous barrier coatings and presents his high-performance systems that result in good to very good barrier values on both paper and film.
Thomas Schmitt reports on monoaxial stretching systems for blown film that stretch at the top of the bubble before the tube is laid flat. This saves energy because the bubble is still warm and increases the degrees of freedom in the process. One advantage is the improved flatness of such films.
Anna Helgert reports on thermoformed packaging that can also be material-reduced in construction. For example, meat can hardly be packaged more minimally in shrink packaging – but of course this is also possible with the thinnest films using barrier coextrudates.
Achim Grefenstein shares his new developments from the modular system, which are all based on monoaxially stretched blown films, with market competitors. We need to quickly achieve significant volume shifts from multi-material to mono-material. For Flexpack, he sees only 3 polymers in the medium term: polyethylene (PE), polypropylene (PP) and polyethylene terephthalate (PET). These films are all based on either PE or PP and can also be combined. The multi-layer, stretched blown film can be supplied – depending on the application – with or without a barrier.
Christian Lutze enlightens the plastics experts about the advantages and disadvantages of paper packaging. Mitsubishi supplies only virgin fibres for the food packaging market and relies on recyclable, water-based systems for barriers, which should not exceed the 5 % foreign matter limit for paper packaging. Oxygen, aroma, fat and water vapour barriers already exist in the medium barrier range. But even in the paper sector, recyclates are only hesitantly used for food packaging – for good reason!
Jochen Moesslein offers a fluorescent tracer not only to mark individual materials or layers, but to make entire recipes identifiable in the recycling stream. A tracer can therefore be provided with an entire recipe – ideally printed on packaging or as a label. The first industrial prototypes have already been developed with Zeiss, and from September recyclers will be able to carry out tests at Polysecure’s technical centre.
Andreas Peterhanwahr offers monitoring and quality assurance systems for regenerated films from a single source. Integration into the machine software and retrofitting are also possible.
Victor Trapp relies on bio-ormocers. This is where the circle closes, he says, referring to the impressive barrier properties of ormoceres – also based on biopolymers. Intensive work is also being done on the price. The fact that ormocers are used, among other things, to refine high and ultra-high barriers proves their raison d’être.
Lars Hancke finally describes the enormous variety of coatings with different barriers against UV light, grease, oxygen and water vapour that a coating and ink manufacturer can offer today. Deinking will also play a role here to make printed films and papers even more recyclable in the future. All together, less material, mono-material build-ups, deinking and a barrier adapted to the application will, in his opinion and the opinion of all participants and speakers, enable the way to a circular economy with barrier films.
We cannot do without them – that is the consensus.
More information and purchase of access data to the recordings and presentations at: innoform-coaching.de/tagung/barriere-verbundfolien-der-expertentreff-2022.
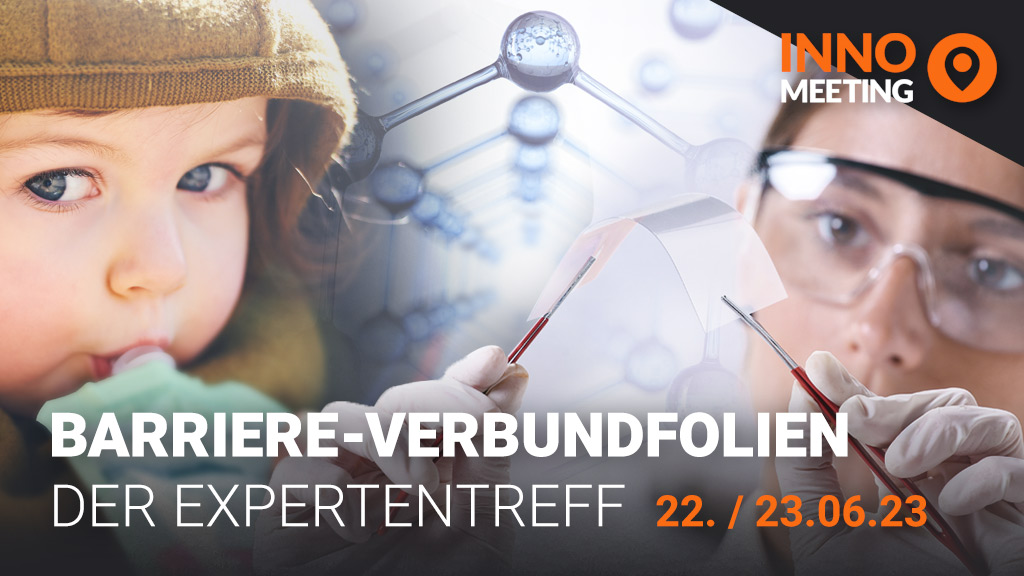
We streamed the summary live on LinkedIn and it is available in German here: https://www.linkedin.com/posts/karstenschroeder_flexpackbranche-skz-innoform-activity-7077962399147786240-UTfI?utm_source=share&utm_medium=member_desktop
Karsten Schröder, June 2023