offered numerous minimal, optimal and ingenious solutions
On 11 and 12 June 2024, the symposium at the SKZ-Modellfabrik Würzburg highlighted five key aspects of environmentally friendly plastic packaging. New, practical solutions for sustainable packaging developments were presented in all areas
Dieter Finna
The event brought together experts from industry, research and brand owners for the fourth time. Karsten Schröder, initiator and moderator of the symposium, analysed the core criteria of environmentally friendly developments together with the speakers. Solutions based on suitable material selection, recyclability, minimisation of material consumption, optimisation of the production process and improvement of product life cycles were presented.
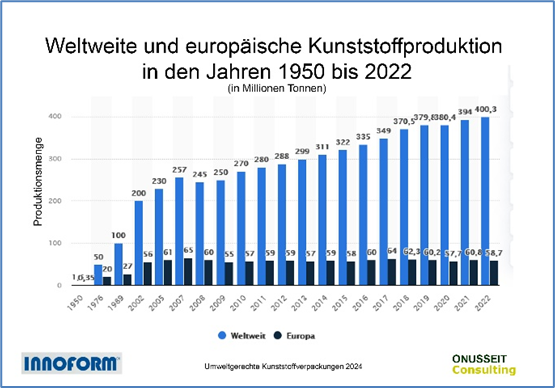
Global and European production of plastics for packaging materials. (Source: Onusseit Consulting)
In his presentation “Quo vadis plastic packaging”, Dr Hermann Onusseit from Onusseit Consulting addressed the challenges posed by the global increase in plastic packaging, which is short-lived as packaging itself (waste) and long-lasting as plastic (microplastics).
A central aspect of the EU Green Deal is the mobilisation of industry for a circular economy. Nevertheless, a third of plastic waste in Germany does not end up in recycling plants. Despite efforts, there is a large gap between theoretical and realistic recycling potential. Onusseit concludes that far more radical measures are needed to achieve environmentally friendly packaging.
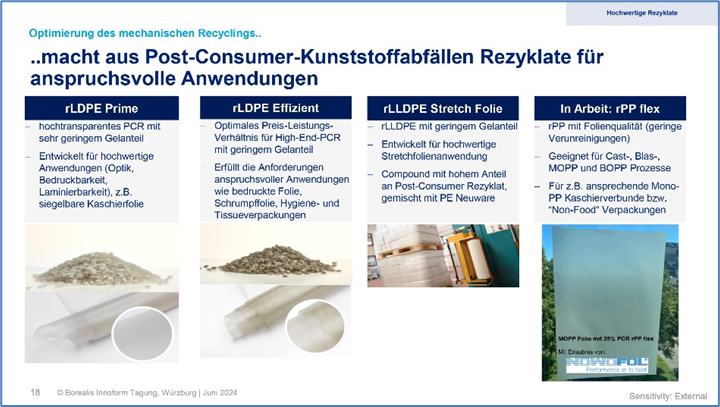
Applications of recyclates in very different packaging applications. (Source: Borealis)
Peter Niedersüss von Borealis Polyolefine GmbH präsentierte den „Einsatz von bio-basierten und recycelten Kunststoffen für flexible Verpackungen“ in Hinblick auf eine funktionierende Kreislaufwirtschaft. Einerseits kommen dafür Polyolefine aus nachwachsenden Rohstoffen zum Einsatz, gewonnen aus Abfall- und Reststoffströmen. Sie bieten die gleiche Materialleistung wie Neuware, aber bei geringerem CO2-Fußabdruck und der Eignung für Lebensmittelkontakt.
On the other hand, recyclates from mechanical recycling, suitable for non-food packaging. They are already used in various qualities for sealable laminating films, hygiene and tissue packaging and stretch film. In the future, PP recyclates in film quality will also be available for laminating composites and non-food packaging.
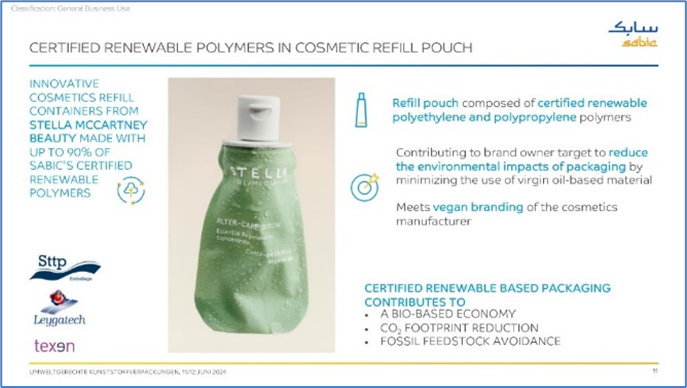
Use of a renewable polymer in a cosmetic refill pouch. (Source: Sabic)
In his presentation “Practical solutions for more sustainable packaging”, Ben Raven from Sabic Petrochemicals BV presented the TruCircle programme, which aims to achieve CO2 neutrality in packaging materials and uses innovative recycling methods. At the Geleen plant (NL), a steam cracker is at the end of the recycling process. The bio-polymers and certified Sabic polymers obtained there replace conventional plastics in numerous packaging applications such as beverage carton packaging or cosmetic refill pouches. Ocean Bound Plastic is also chemically recycled in Geleen and integrated into TruCircle packaging materials.
In his presentation “Sustainable PE films: Improved life cycle assessment through holistic development approaches”, Lutz Neugebauer from packaging manufacturer Südpack identified the infeed materials and the recycling method as the biggest factors influencing the life cycle assessment of plastic packaging. Substituting multi-layer structures with recyclable single-material solutions reduces the carbon footprint of both the infeed materials and mechanical recycling. However, the primary quality of raw materials can only be recovered through chemical recycling. The use of recyclates helps to further optimise the life cycle assessment.
Dr. In his presentation “Digital product passport – proof of recyclate – CO2 footprint”, Hermann Achenbach from SKZ – Das Kunststoff-Zentrum demonstrated the specific benefits of the COPPA digital product passport for food packaging. Against the backdrop of changing regulations, this creates the necessary transparency by providing detailed digital information about the materials and components of the packaging. It supports the circular economy and improves sustainability by providing all stakeholders – including the consumer – with relevant data for proper disposal and recycling. A key new component of this research project is the identification of individual data sources. This makes the product passport more robust and credible.
The SKZ invites interested companies to have COPPA create free prototypes of digital product passports.
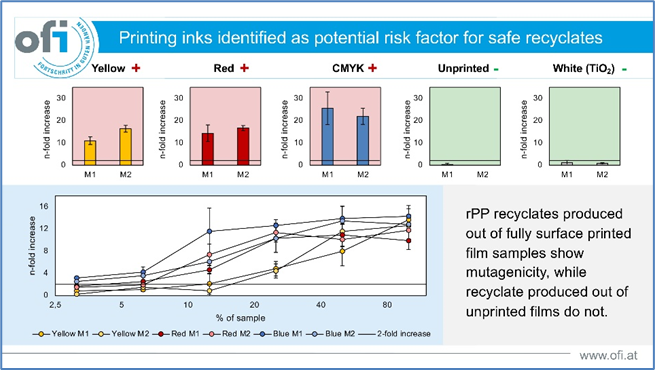
Nitrocellulose-based printing inks as a potential risk factor for safe recyclates. (Source: OFI)
In his presentation “Safety assessment of unknown contaminants in recycling”, Dr Christian Kirchnawy from the Austrian Research Institute for Chemistry and Technology explained the risks of unidentifiable pollutants in mechanical recycling. DNA-reactive, mutagenic substances play a special role in the safety assessment, as these have 120 times lower threshold values than all other substances in the EFSA safety assessment in accordance with the Threshold of Toxicological Concern. Some recycled polyolefins – which are not yet authorised for food contact – show clear mutagenicity. Granulates show higher mutagenicity signals than flakes. This indicates that harmful substances are primarily formed during extrusion. PP recyclates from printed films with nitrocellulose inks are strongly positive in the mutagenicity test, which identifies these printing inks as a potential risk factor for mutagens in these regranulates. Delabelling or deinking processes in PP or PE recycling would therefore be helpful. Good to know: no DNA-reactive impurities have been detected in food-safe recycled polyester (PET).
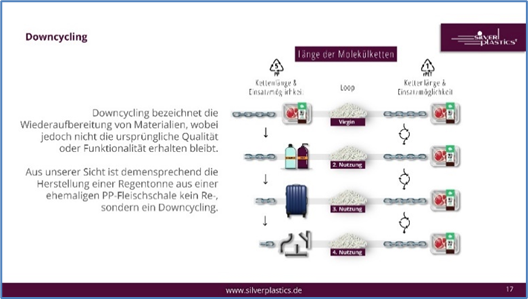
PET trays can be used several times for food packaging, while PP trays are subject to downcycling. (Source: Silver Plastics GmbH & Co. KG)
Christopher Tuchscherer from Silver Plastics GmbH & Co KG compared the barrier and recycling properties of both materials in his presentation “PET vs PP trays – advantages and disadvantages”. Europe has extensive recycling options for PP moulded trays, whereas these still need to be developed for PET trays. PET trays can be reused several times for food packaging, while PP trays are only recycled in non-food applications. The mono PET moulded tray “Capirella” is equipped with a capillary base, which makes glued-in absorbent inserts superfluous and makes the tray fully recyclable, which is not yet possible with PP trays.
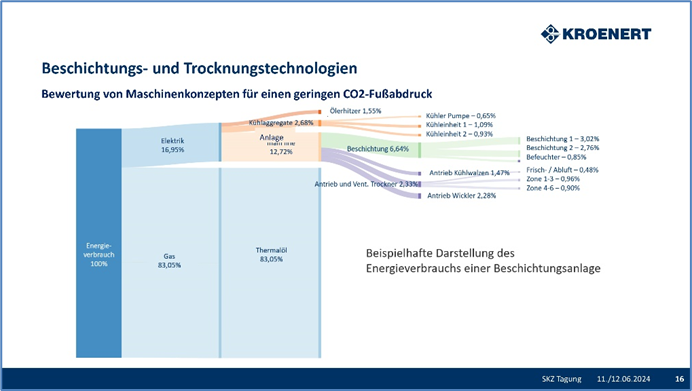
Drying accounts for over 80% of the energy required for coating systems. (Source: Kroenert)
Andrea Glawe of Kroenert GmbH & Co KG presented modern approaches to increasing energy efficiency in her presentation “Optimising the design of coating systems to reduce energy consumption and emissions”. As the dryer accounts for more than 80% of energy consumption in coating systems, energy-saving wet-on-wet applications and simultaneous double-sided coating processes have been developed. In addition, heat exchangers and heat recovery systems are used to pre-heat fresh air. Customers are provided with an energy footprint that shows the kWh consumption per square metre and offers the possibility to determine the total CO2 footprint of the product. But even small measures such as energy recovery during processing have an impact. In his presentation “Virtual production assistance – prerequisites, opportunities and benefits”, Dr Kenny Saul of SHS plus GmbH highlighted the challenges and benefits of digitalisation in extrusion processes. Firstly, the machine control system must be able to communicate “externally”. Machine control is optimised by collecting process and job data. The data is analysed in real time using statistics and AI support, with a recommendation algorithm categorising errors and offering solutions based on learned patterns. The integration of the R-Cycle connection enables the creation of digital product passports for global traceability of plastic products (see presentation by Achenbach – SKZ).Andrea Glawe from Kroenert GmbH & Co KG presented modern approaches to increasing energy efficiency in her lecture “Optimising the design of coating systems to reduce energy consumption and emissions”. As the dryer in coating systems accounts for over 80% of energy consumption, energy-saving wet-on-wet applications and simultaneous double-sided coating processes have been developed. In addition, heat exchangers and heat recovery systems are used to preheat the fresh air. Customers receive an energy footprint that indicates the kWh consumption per square metre and offers the possibility of determining the entire product CO2 footprint. But even small measures such as energy recovery during processing have an impact. In his presentation “Virtual production assistance – prerequisites, opportunities and benefits”, Dr Kenny Saul from SHS plus GmbH highlighted the challenges and benefits of digitalisation in extrusion processes. Firstly, the machine control system must be enabled to communicate “externally”. The control of the machines is optimised by recording process and order data. The data is analysed in real time using statistics and AI support, with a recommendation algorithm categorising errors and offering suggested solutions based on learned patterns. The integration of the R-Cycle connection enables the creation of digital product passports for the global traceability of plastic products (see presentation by Achenbach – SKZ).
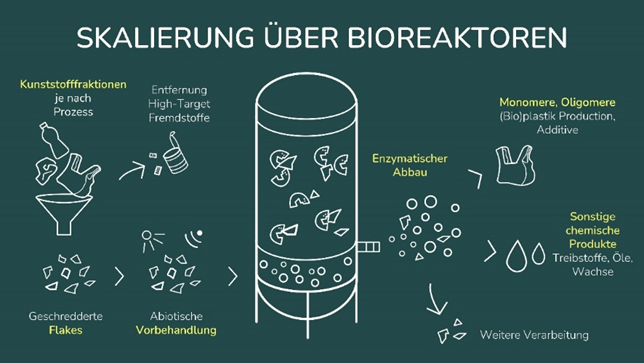
Scaling of enzymatic recycling via bioreactors. (Source: M.I.L.K. GmbH)
In her presentation “Plastic as a nutrient – the potential of enzymatic recycling”, Eleonore Eisath from MILK. GmbH explained how enzymes can be used to break down the long molecular chains of plastics in packaging into monomers and oligomers in order to use them as a raw material for the production of new materials. The prerequisite for this is that specific enzymes are identified for the different types of plastic and optimized using protein engineering methods, which is a complex and cost-intensive process. Enzymatic recycling is currently in the development phase – while the first pilot plants are already under construction for PET, development for PE will still take several years and the process will not be usable before 2030. The search for suitable proteins is being accelerated by AI models, among other things, which can use simulations to identify shortcuts in research.
Andreas Holt – today-tomorrow-together presented various optimization potentials in extrusion technology in his lecture “Production process: reducing energy consumption and emissions”. He discussed the advantages of gravimetric systems for the precise dosing of regrind from recyclates and the simplified reuse of production materials.
A fully automatic material cleaning system enables material changes without operator intervention and reduces the changeover times of an extrusion line. A speed-controlled conveyor system improves transport performance and saves considerable energy with minimal vacuum. The SMART manifold system presented enables sequential material allocation, shortens changeover time, checks recipes to avoid incorrect batches and reduces installation costs for lines.
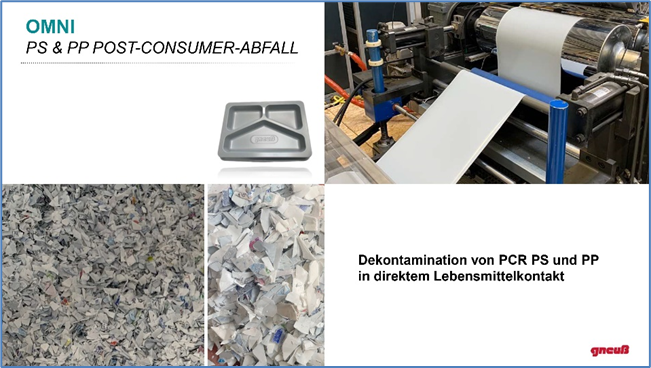
Film production from polystyrene and polypropylene post-consumer waste. (Source: Gneuss Kunststofftechnik GmbH)
Niklas Möhlmann from Gneuss Kunststofftechnik GmbH presented the OMNI recycling technology in his lecture “Innovative mechanical recycling process for food packaging made from post-consumer plastics”. This technology processes a wide range of plastic materials, including highly contaminated and heterogeneous polyolefins. In the first step, a cutter compactor compacts the regrind. Advanced filtration and degassing techniques ensure a high quality of the recycled material. Contaminants in the melt are largely separated and degassed using the multi-shaft concept. Möhlmann demonstrated this using two case studies in which PET tray waste and PS and PP post-consumer waste were recycled. The resulting films are decontaminated and have food approval for post-consumer plastics. There are already FDA approvals for PP in Asia – that gives us hope.
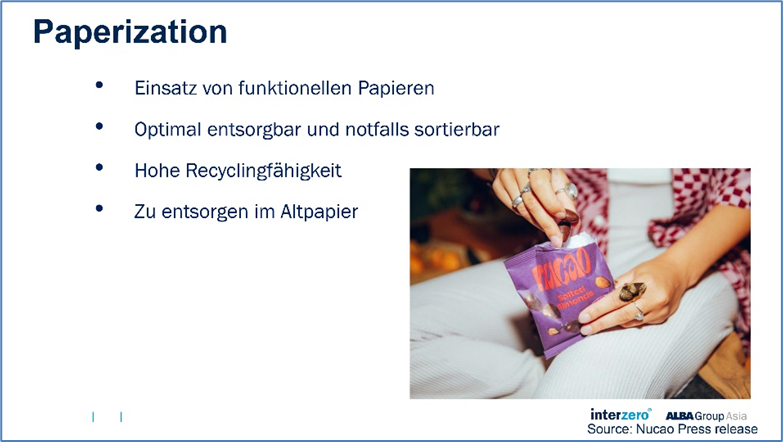
The choice of packaging material, in this case paper, determines the disposal fees. (Source: Interzero Recycling Alliance GmbH)
Julian Thielen from Interzero Recycling Alliance GmbH highlighted the concept of eco-fee modulation in his presentation “Saving disposal costs through intelligent film design”. In various countries, this concept penalizes the use of packaging materials that are difficult to recycle through higher fees. As the national dual systems in Europe set the tariffs based on their respective collection, sorting and recycling infrastructure, the greatest savings potential lies in material reduction. Examples include coffee packaging made from mono-material PE, which replaces PET/Alu/PE composites, detergent packaging made from molded PP with a recyclate content of 92% and paper packaging.
Thomas Lunz from Mondi Functional Paper & Films gave an overview of the use of fiber-based flexible packaging materials in his presentation “Packaging made of paper”. 95/5 papers made from 95% paper and max. 5% mostly polyolefins, which can be recycled as a mono-material in waste paper streams, are particularly popular. Barrier papers with different barrier properties for dry food, ice cream, confectionery, health & personal care, etc. can be produced using both dispersion and extrusion coating. High-barrier papers with metallization also offer solutions for very demanding barrier applications, so that coffee, spices, washing powder, etc. can be packaged in them. They are also certified for the paper cycle. So: paper where possible, plastic where necessary.
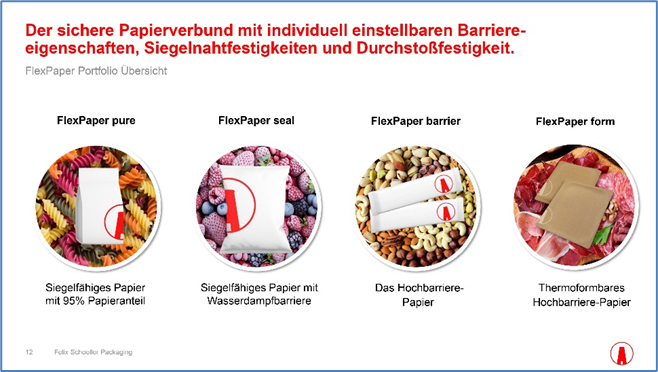
The portfolio of packaging papers ranges from sealable to high-barrier variants, supplemented by thermoformable high-barrier papers. (Source Felix Schoeller)
Andreas Bergmeier from Felix Schoeller GmbH & Co. KG gave an overview of the possibilities and limitations of paper packaging in his presentation “Barrier papers for Flexpack”. He made it clear how imprecise and flexible the material specification of 95% paper content is, which serves as a criterion for classification as a mono-material. There is also a need for clarification regarding collection systems for flexible paper packaging, which should formally be collected correctly in the yellow garbage can, but is contaminated there and cannot be recycled. A better solution is to collect it via waste paper.
Felix Schöller’s FlexPaper portfolio, which ranges from sealable variants to high-barrier papers with high water vapor and oxygen impermeability, also includes a thermoformable high-barrier paper that replaces plastic forming trays and, with a paper content of over 90%, is very easy to recycle.
Felix Bischopink from Siegwerk Ventures GmbH addressed the needs of SMEs in his presentation “Sustainable packaging innovations through digital platforms”. He emphasized that companies often have too high expectations of innovations and underestimate the initial phase. The Packiro platform serves as a partner for printed, sustainable packaging solutions and is based on four principles: Focus on innovative retailers and producers, digital processes from purchase to production, small unit quantities through digital printing and sustainable packaging. According to Bischopink, Packiro shortens the time from planning to market launch of packaging from 1-3 years to 1-3 months.
Karsten Schröder concluded the symposium with his concise summary of practical solutions. The use of renewable raw materials and the further development of packaging materials make a significant contribution to sustainability. In the production of packaging materials, developments in machine and control technology are reducing their CO2 footprint. And improvements in mechanical recycling and extrusion technology, slightly growing chemical recycling and new processes such as enzymatic recycling are playing a key role in the processing of packaging today or will do so in the future
An optimistic outlook, considering how great the challenges are overall, to which packaging can make a small contribution. However, flexible packaging is always sustainable because it protects the contents, concluded Karsten Schröder with a quote from Hermann Onusseit’s opening presentation.
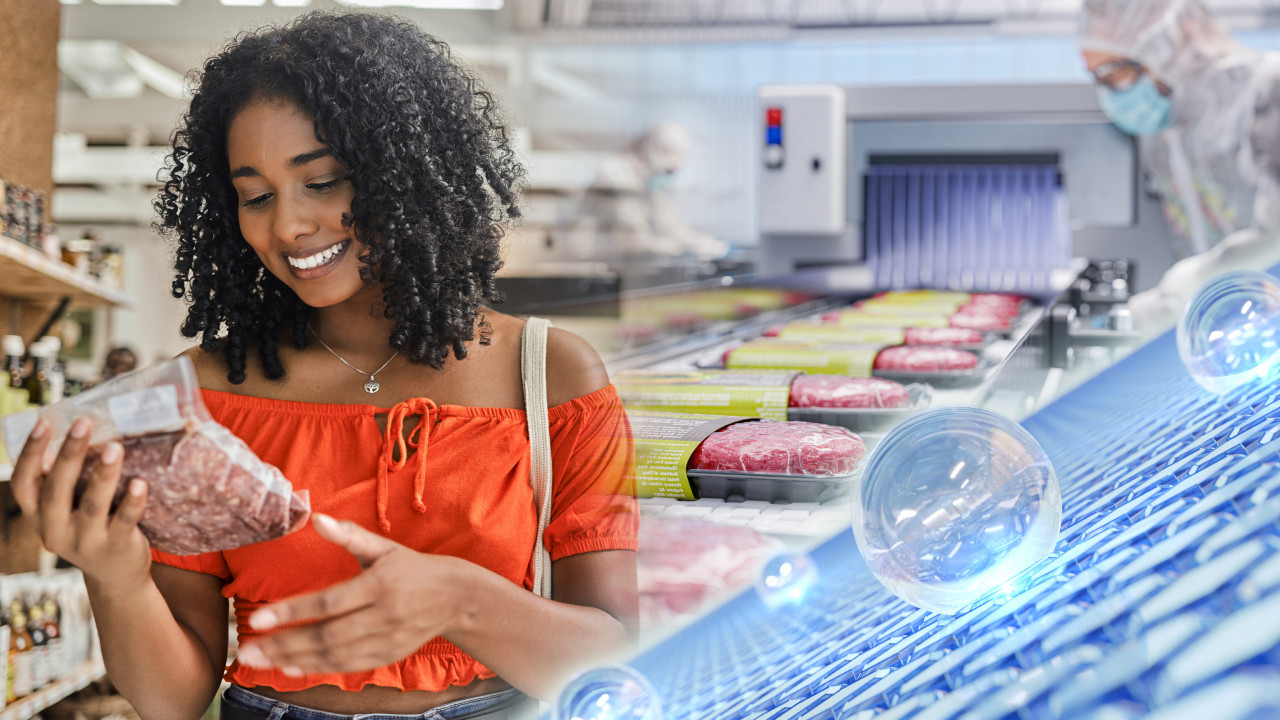
22. Inno-Meeting: Minimalverpackung Flexpack – Trends und Technologien 2025
Wednesday, 12. / Thursday, 13. February 2025 – 9:30
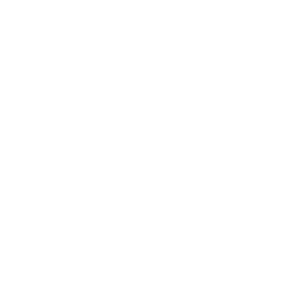
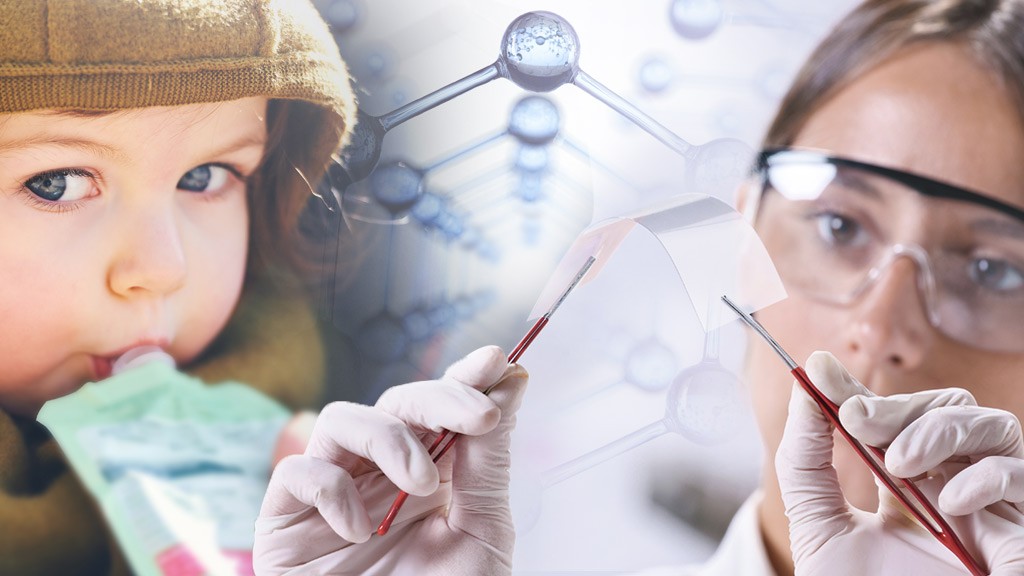
Barrier laminates – The expert meeting
Tuesday, 1. / Wednesday, 2. July 2025 – 9:00
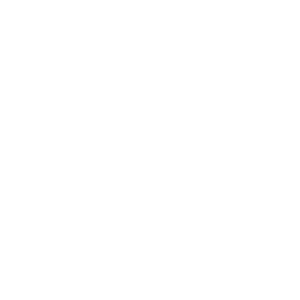